随着电子产品小型化、智能化、多样化的发展,给产品热设计带来了更严峻的挑战。一方面,随着边缘计算和人工智能的发展,让算力更为密集;另一方面,随着双碳目标迫近,对于功率等级要求也持续提高;因此单一设备的功率密度正在不断攀升,热功率也相应的随之提高,而热设计也就受到了越来越多的关注。
热设计的必要性和挑战
所谓热设计(Thermal Design),是指在工程设计中考虑和优化热传导、热辐射和热对流等热学因素的过程。它主要涉及如何有效地管理和控制热量,以确保设备、系统或产品在运行时能够正常工作并满足性能要求。
热设计通常应用于各种领域,包括电子设备、汽车、航空航天、能源系统等。在这些应用中,热设计的目标是防止过热或过冷,维持适当的工作温度范围,以避免设备损坏、性能下降或故障。

图1:电子产品热设计的重要性(图源:GEC研究院)
如上图所示,从芯片角度来看,根据GEC研究院的数据,节点寿命会随着节点温度提升而大幅降低,失效率加速。从系统角度来看,根据美国空军航空电子整体研究项目的结论,55%的设备故障原因来自于温度因素。
因此温度可以说是电子设备的第一大杀手,设备的电气性能和热分布会相互影响:温度过高会导致电子产品的绝缘性能退化,电阻降低,材料老化;像处理器、变压器等芯片,高温会使其性能下降;进一步的高温会造成元器件功能失效。
不良的热设计会导致系统内部产生更多高电流浪涌,导致系统中被引入了主要芯片之外的额外热源。为了处理好这些不利热点的影响,保证产品的稳定运行,就不得不额外增加温度控制功能,从而增加了额外的能耗。做好热设计,不但能让产品更稳定,也是系统节能的关键一环。
热设计软件制造商Future Facilities(已于2022年被Cadence收购)的研究发现,新的热设计重点将主要由人工智能、物联网、5G和边缘计算等技术推动。Future Facilities产品经理Chris Aldham曾表示:
过去几年技术的进步导致工程师看待热设计的方式发生了前所未有的变化。人工智能、5G、边缘计算和物联网的引入都对电子产品的运行方式和地点产生了重大影响,而这反过来又意味着从热学角度需要考虑一系列新的因素。

图2:电源系统性能和热管理息息相关(图源:Molex)
当前对于电子产品而言,热设计的挑战来自方方面面。
1. 小型化
小型化带来的计算密度和功率密度的提升,而且小型化同时也就意味着需要尽量采用无风扇或者小型风扇的设计,这直接对于系统散热设计提出了更高的要求。
2. 信号传输
系统中的信号处理速度越来越快,这种高速信号的传输和处理也会产生更多的热量。
3. 屏蔽设计
当前的系统中,为了保证信号的完整性会采用更多的屏蔽设计,这种屏蔽设计本身对于散热就产生了不利的影响。
而上述提到的挑战仅仅来自于设备内部,还有更过设备外部环境因素需要考虑:像数据中心、储能站等设备排布密集的工作环境,各个设备之间相互的热辐射就很大;而一些高海拔地区的设备,由于工作环境空气稀薄,因此对于设备散热要求也就更高。
再深入到芯片设计的领域来看热量管理的挑战:为了维持单位面积上算力的提升,3D封装芯片成为芯片设计的必然趋势。而这种3D堆叠的结构会产生高热阻,且在不同芯片功耗不均匀情况下更易导致热点、高温梯度和热应力等热问题。硅通孔(TSV)被认为是降低3D IC温度的有效手段,因此被广泛使用。
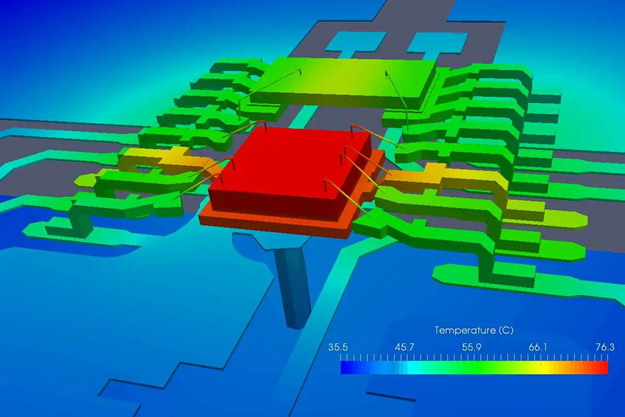
图3:3D封装芯片内部金属互联结构的温度分布图(图源:Cadence)
传统上来说热设计是一门小众的细分领域,通常是由具备热传递知识背景的机械工程师,为所有的业务部门提供热设计服务。
在那时候热设计更多和机械部分相关,和电子部分是分开独立进行的。而在现在,随着设备越来越小型化和高功能化,热设计与整个系统的性能和可靠性表现愈发密切,需要从产品的原型设计阶段就进行热设计的考量。热设计工程师除了必备热知识背景外,还应具备机械、电气和电子背景,能够熟练使用EDA设计工具和各种仿真工具,与电子设计团队并行进行热设计。

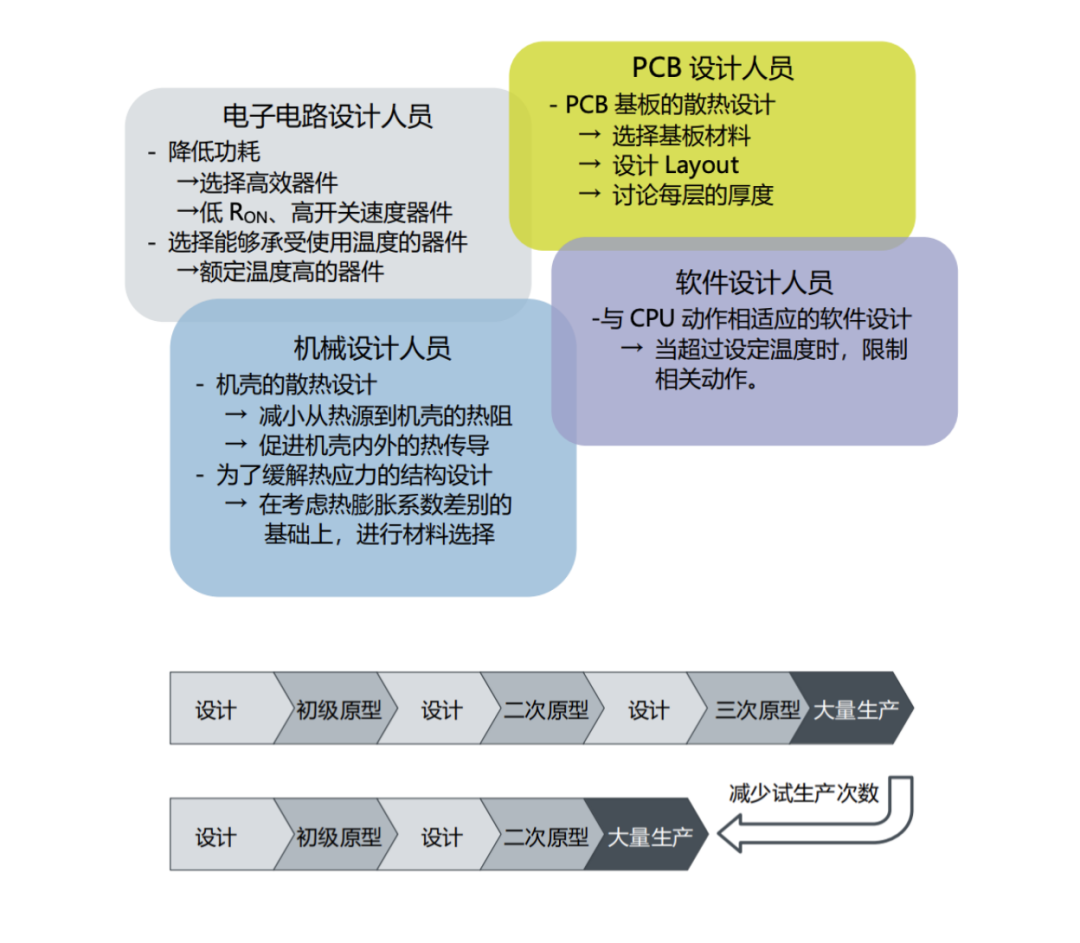
图4:各设计部门共同减少发热量,减少试生产次数(图源:ROHM Semiconductor)
好的热设计,从选型开始
芯片厂商同样需要重视热量管理,通过优化芯片热性能可以实现整个系统功率密度的突破。
1. 工艺制程创新
首先是通过工艺制程的创新来增强热性能。例如在减少芯片体积的同时尽量减少功率器件的导通电阻;或通过新的工艺节点来优化引脚布局并提供额外接地等。
2. 芯片设计
其次在芯片设计方面,可以将温度监控功能集成到关键芯片的内部,通过高效的开关来实现不同工作负载下的动态调节,为高度集成的电路设计实现更高的功率。在封装方面,可以通过创新的封装方式,例如加大引脚面积、优化引脚材质和设计等,来实现芯片更高的散热效率。
3. 方案设计
从方案设计角度来看,要优化整个系统的热传导路径。例如像一些顶部散热功率芯片,近年来也逐渐流行,选择此类芯片能够减少热量向PCB的直接传导,通过芯片顶部直接将热量辐射或传导到设备外壳外。

图5:Apple申请的自适应热控制系统专利(图源:https://appft1.uspto.gov)
总体而言,好的热设计需要从系统整体来考虑,从芯片选型的阶段就将热设计目标考虑在内。芯片、连接器和PCB都要根据整体的热指标来进行选择或设计,其中连接器等接插件的好坏对热设计非常重要,选择具有良好热管理的连接器芯片,能够直接帮助优化整个系统的热设计。
接下来,就为大家推荐几款来自Molex的具有优秀热设计特点的连接器产品。
首先在电源连接器的选择上,可以考虑Molex的PowerWize大电流互连系统。这是一款大电流线对板/线对母线互连系统,双电路插头和插座外壳提供两种尺寸:6mm(额定电流高达120A)和8mm(额定电流高达175A)。
热设计方面的优势在于该器件采用低接触电阻和低压降设计,极大限度地减少了触点接口的热量生成。此外,更高的额定电流和更紧凑的外形设计,也就意味着该器件能够支持更高功率密度的产品设计。
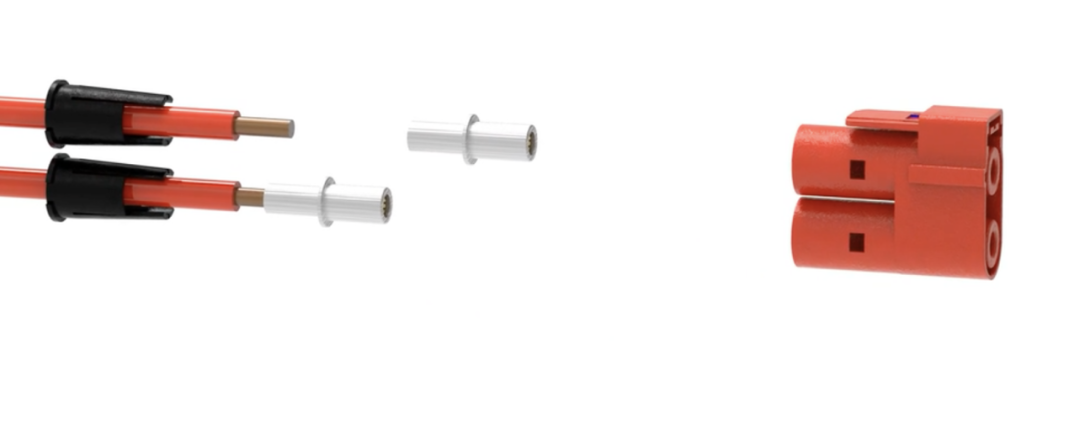
图6:Molex的PowerWize大电流互连系统(图源:贸泽电子)
对于热设计而言,热敏电阻是必不可少的热管理器件之一。Molex提供的NTC热敏电阻探头采用了独特的柔性设计,能够适用于在难以触及的位置提供准确的温度读数。
此外,该器件提供了高达1.5KVAC的介电耐压,能够持续3秒;在500VDC时能够实现高达100MΩ的绝缘电阻;正常工作温度范围支持-40°C至250°C。良好的抗高压和宽广的温度范围支持其在任何严苛的设计中正常工作。
在设计自由度方面,该器件预留可直接焊接到PCB板并装配到接线板的自由端电线,这些末端电线还可压接到端子上,并与连接器一起使用,从而为设计人员提供了更多灵活的设计选项。

图7:Molex NTC热敏电阻探头(图源:Molex)
最后再给大家推荐一款同样是来自Molex的连接器——VersaBlade线对线连接器系统。该器件能够在系统中实现300V和15.0A的可靠信号和电源传输,并具有防止误插配和导致信号故障的特性。
在散热设计方面,该器件采用了双排系统设计,有助于加速散热并实现较小的结合力。此外,具有灼热丝功能的外壳符合全球安全和环保要求。

图8:Molex VersaBlade线对线连接器系统(图源:Molex)
结语
随着产品功能要求的不断提升,导致设备内部元器件贴装更为密集,发热量也随着计算和功率密度同步增加,散热设计却因为设备外型限制而变得更加困难。因此,要实现优良的热设计,提高整个设备的热效率,要尽早开始着手考虑,在产品设计的原型阶段,就要开始规划系统整体的散热策略,并在器件选型过程中,就充分考虑整个系统的热设计目标对于单一器件的热功率要求。好的热设计,应从器件选型开始。
本文转载自: 贸泽电子微信公众号